CASE Visualization of the inside of a major beverage manufacturer’s factory using business cameras
CUSTOMER
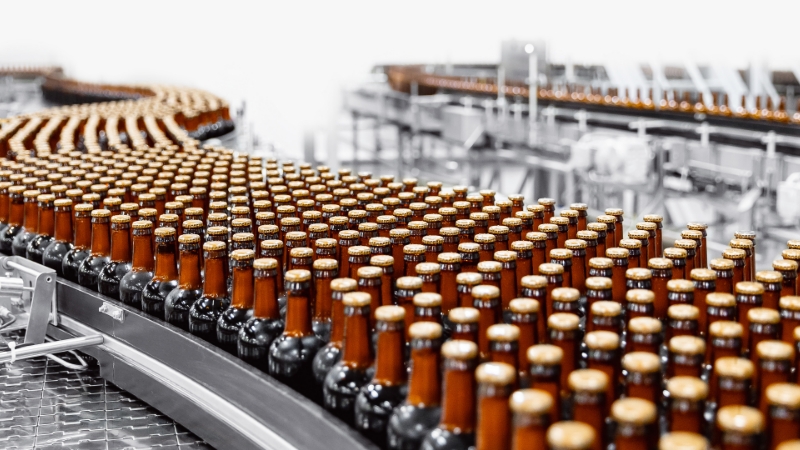
Major beverage manufacturer
Visualizing the manufacturing process saved 1,000 work hours per year
This major beverage manufacturer was using cameras in their production lines. However, their management software was not easy to use and was not being utilized in operations.
They needed many workers and hours to address issues and to investigate the root cause on the manufacturing floors.
To address this issue, they introduced RYODEN’s camera system for reducing human power by leveraging images from cameras and for improving work efficiency.
As a result, it has become possible to get an understanding of where an issue has occurred without dispatching a worker to the site.
BACKGROUND
Challenges faced by widely automated food and beverage manufacturers
Modern food and beverage plants have adopted automation and the use of IoT to be operated by a small number of people.
However, in reality, a large number of people and much time are needed to respond to facility troubles and to look into their causes.
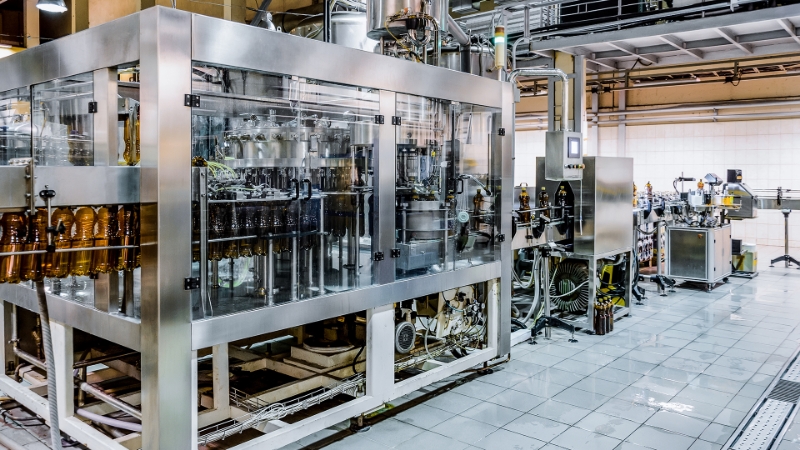
Wider use of camera images
While this major food and beverage manufacturer has introduced a camera system, it was operating independently without being linked to the rest of the facilities.
As a result, images from the cameras had limited uses.
reason
Visualization of plant floors made operation by a small number of people possible
The plant wanted to use cameras, rather than people, to monitor the plant. They would like to achieve a higher efficiency in operation.
To this end, they wanted a viewer for real-time and past images that anyone could operate, as well as a system to link various sensing information in the plant to camera images.
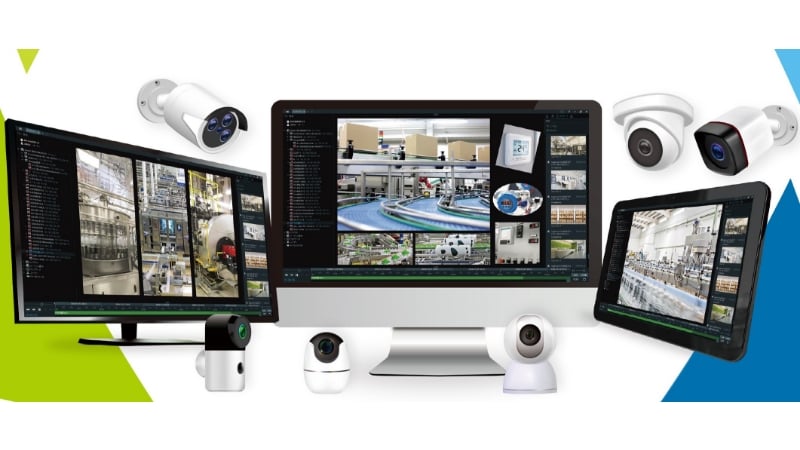
Quality Assurance - Efficient Monitoring
We were spending a lot of man power and time to look into finding causes when troubles occurred on our production lines such as cans and bottles falling and printing errors.
We were also spending a lot of time sharing information between the plant floors and production management. We were looking for a system to solve these challenges.
benefits
Labor savings equivalent to 1,000 hours per year per plant
Utilizing images from cameras installed on the production floors enabled us to monitor the facilities without traveling in the large plants.
This made it easier to discover troubles at an early stage and to look into their causes, which led to improving working conditions for operators and to reducing human labor.
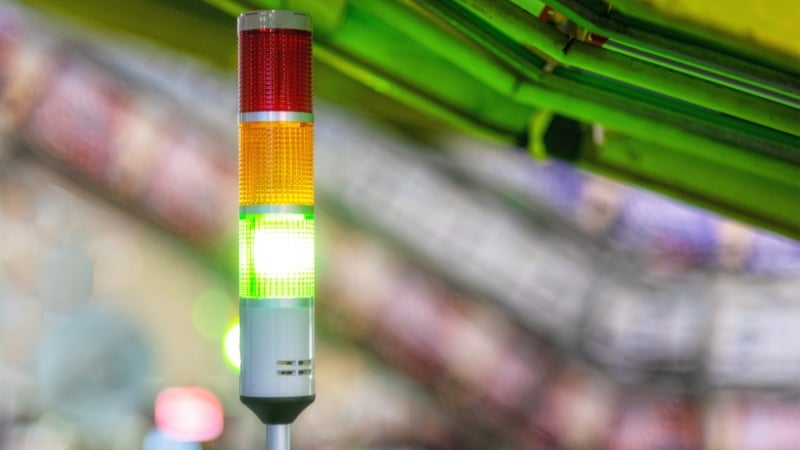
Facilitated discovery by linking between camera system and PLC
When a trouble occurs on the production line of cans or bottles, the camera system links to the PLC (sequencer) to notify the production manager.
Monitoring the situation using images enabled providing appropriate instructions to the operators on the plant floor. Furthermore, this enabled quick reviewing of what happened before and after an incident. Additionally, use of tablets in the wireless environment made it possible for operators on the plant floor to monitor in real time, thus improving work efficiency.